Magnetic Particle Inspection (MPI)
Magnetic Particle Inspection (MPI) likewise sometimes called as Magnetic Test (MT) is a non-ruinous test strategy for the detection of surface and sub-surface discontinuities in ferrous materials. The test technique includes application of magnetic field remotely or applying electric current through the material which thus creates magnetic transition in the material. At the same time, noticeable ferrous particles on sprinkled or splashed on the test surface. The nearness of a surface or close surface discontinuities in the material causes distortion in the magnetic transition which thusly causes spillage of the magnetic fields at the discontinuity. The magnetic particles are pulled in by the surface field in the zone of the discontinuity and cling to the edges of the discontinuity showing up the state of the discontinuity.
Magnetic Particle Testing to Find Defects in Magnetic Parts
This reference guide will give you a general review of performing Non-damaging Testing by the magnetic particle technique. The utilization of this technique brings about discovering abandons which are not generally unmistakable to the eye. By utilizing types of gear, materials, and embellishments you can find such intrinsic and processing abandons as: inclusions, creases, lamination’s, recoils, cracks, hot tears, laps, drops, welding absconds, warm treat and pounding cracks, machining tears, extinguishing and fixing cracks and also service cracks on parts from benefit.
This inspection is important to the quality of the finished product, and in finding defects as early as possible in manufacturing, to avoid wasting machining and processing time on defective material.
Advantages and Disadvantages Magnetic Particle Inspection:
Advantages:
- Magnetic Particle Inspection generally is compact. Also, can in this way be utilized as a part of a workshop or on location.
- It’s a reasonable strategy contrasted with Radiography or Ultrasonics
- Little or substantial things can be assessed, additionally complex parts can be investigated rapidly.
- The test method process is quick and simple in principle and application; only a moderate level of skill is required.
- Quick Results and don’t require any waiting time, similar to Radiography or Dye Penetrant Inspection (DPI).
- It can find surface and close surface signs, these have a tendency to be the most essential since that is the place the anxieties think.
- The surface ought to be spotless, however this isn’t as basic as Dye Penetrant Inspection
Disadvantages:
- Needs an electric supply, which can hinder its versatility
- Can be indistinct regardless of whether the magnetic field is sufficient to demonstrate signs effectively
- More often than not paint should be evacuated before inspection
- Can’t be utilized to tests parts that not ferromagnetic i.e. stainless steels
- Can be untidy, particularly in limited spaces
- Fake signs are a risk, particularly between two divergent materials
- The vapor from the paint can make a fire danger, particularly in limited spacesMust be mindful so as not to utilize Magnetic Particle Inspection where the magnetic field can harm different instruments
- Demagnetization and post cleaning is here and there a necessity
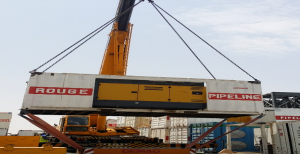
Write a Comment